How important is understanding tension in materials?
Have you ever wondered why bridges don’t just snap under heavy traffic or how cranes lift massive loads without breaking? The answer lies in a key engineering concept—tension.
Tension is the force that stretches a material when pulled apart. Definitely Tension plays a crucial role in everything from steel cables in suspension bridges to reinforced concrete beams in buildings. If engineers don’t account for it properly, structures can crack, fail, or even collapse—just like what happened in the Tacoma Narrows Bridge disaster in 1940.
In simple terms, tension is all about how a material handles pulling forces. Mathematically, it’s defined as
Tensile Stress(σ)= Force(F) / Cross-Sectional Area(A)
This equation helps engineers figure out how much force a material can handle before it stretches too much or breaks. Materials like steel – carbon fiber and high-strength alloys are often used in designs where tension is a major factor.
Understanding tension isn’t just about theory—it’s the backbone of safe and efficient engineering. Whether you’re designing a skyscraper, a suspension bridge, or even a simple truss—knowing how materials react to tension can make all the difference.
Let’s break it down further and explore real-world applications, failures, and key engineering principles that make tension one of the most critical forces in structural design.
What is Tension (Tensile Stress)?
Tensile stress is the internal force per unit area within a material when it is subjected to a pulling or stretching force. It is the opposite of compressive stress, which occurs when a material is squeezed.
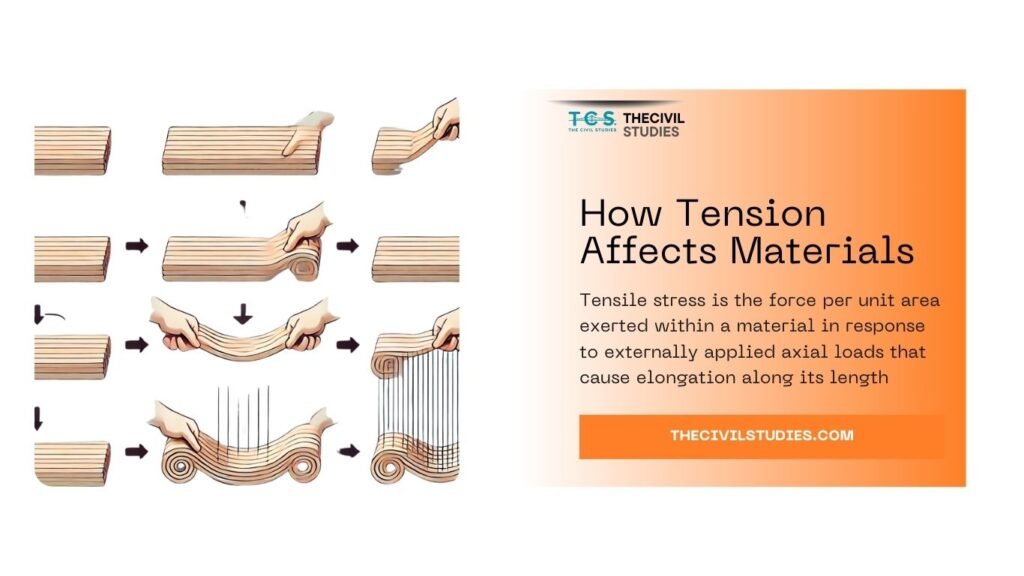
Standard Definition:
“Tensile stress is the force per unit area exerted within a material in response to externally applied axial loads that cause elongation along its length.”
In simpler terms, tensile stress occurs when forces pull outward on an object, stretching it apart rather than compressing it inward.
Key Difference from Compressive Stress:
- Tensile stress → Stretches a material (Pulling apart forces)
- Compressive stress → Squashes a material (Pushing inward forces)
Mathematical Representation of Tensile Stress
Tensile stress (σ) is quantified mathematically as:
σ= F/A
Where:
- σ (Tensile Stress): Force per unit area (N/m² or Pascal, Pa)
- F (Applied Force): The external pulling force acting on the material (Newtons, N)
- A (Cross-sectional Area): The area over which the force is distributed (m²)
Why is Tension Important?
Understanding tension is critical in – Civil, Mechanical and Aerospace engineering. Every structure—whether it’s a bridge, airplane wing, crane cable, or even human tendons—experiences tensile forces. If these forces exceed a material’s ultimate tensile strength (UTS), failure occurs
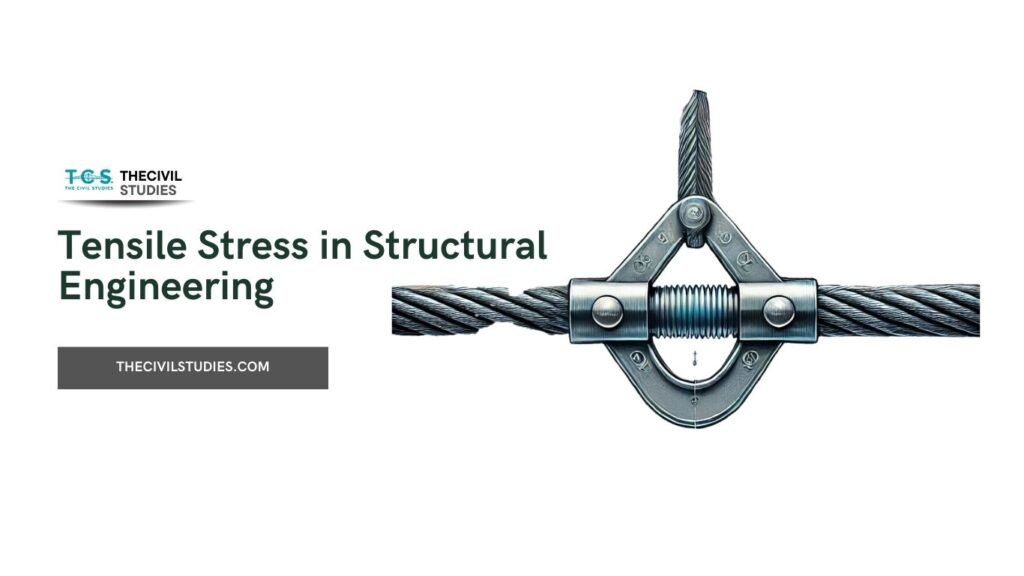
Real-World Example
Think of a suspension bridge like the Golden Gate Bridge. The steel cables supporting the bridge experience massive tensile forces as they hold up the deck. Engineers must carefully calculate tensile stress to ensure the cables don’t snap under extreme loads like high winds or traffic – weight.
Tensile Stress Calculation Example
Imagine a steel rod with a cross-sectional area of 0.005 m² experiencing a tensile force of 1000 N.
Formula:
σ = F / A = 1000 N / 0.005 m² = 200,000 Pa (or 200 kPa)
This means the steel rod is experiencing a tensile stress of 200 kPa due to the applied force.
Key Engineering Concepts
Tensile Strain (epsilonε) – How Much a Material Stretches
Tensile strain measures how much a material elongates under tension compared to its original length:
ε= ΔL/L
Where:
- ε = Strain (dimensionless, no unit)
- ΔL = Change in length due to stretching (m)
- L= Original length of the material (m)
📌 Think of a Rubber Band! When you stretch it, it elongates, demonstrating tensile strain.
Young’s Modulus (E) – Stiffness of a Material
Young’s Modulus (also called the Modulus of Elasticity) measures a material’s stiffness—how much it resists deformation under tensile stress.
E= σ/ε
Where:
- E = Young’s Modulus (GPa or N/m²)
- σ = Tensile Stress (N/m²)
- ε = Tensile Strain (dimensionless)
📌 Example: Steel has a high Young’s Modulus (~200 GPa), meaning it’s very stiff and doesn’t stretch easily. Rubber, on the other hand, has a low Young’s Modulus, making it very flexible.
Ultimate Tensile Strength (UTS) – Breaking Point of a Material
The Ultimate Tensile Strength (UTS) is the maximum stress a material can withstand before breaking. Engineers use UTS to select safe materials for structures and machines.
Example:
- Mild Steel UTS: ~400 MPa
- Titanium UTS: ~900 MPa
- Carbon Fiber UTS: ~2000 MPa (Extremely strong and lightweight)
Quick Reference Table – Essential Formulas
Concept | Formula | Units | Key Insight |
---|---|---|---|
Tensile Stress | σ = F / A | N/m² (Pa) | Force per unit area |
Tensile Strain | ε = ΔL / L | No unit (ratio) | How much a material stretches |
Young’s Modulus | E = σ / ε | GPa (N/m²) | Stiffness of a material |
Ultimate Tensile Strength | UTS = F max / A | MPa (N/mm²) | Max stress before breaking |
Importance of Tension in Engineering
Let’s break it down across different engineering disciplines:
Civil Engineering – How Tension Holds Our Cities Together
Without considering tensile stress, some of the world’s most iconic structures wouldn’t exist.
- Suspension bridges like the Golden Gate Bridge rely on high-strength steel cables under constant tension to support the roadway. The cables must endure wind forces, traffic loads, and thermal expansion—any weakness could lead to disaster.
- Pre-stressed concrete beams, used in modern construction, embed steel tendons in concrete, ensuring the material can withstand tensile forces despite concrete’s natural weakness in tension.
- Skyscrapers use steel-reinforced concrete and high-tensile-strength steel beams to resist both compression (from weight) and tension (from wind and seismic activity).
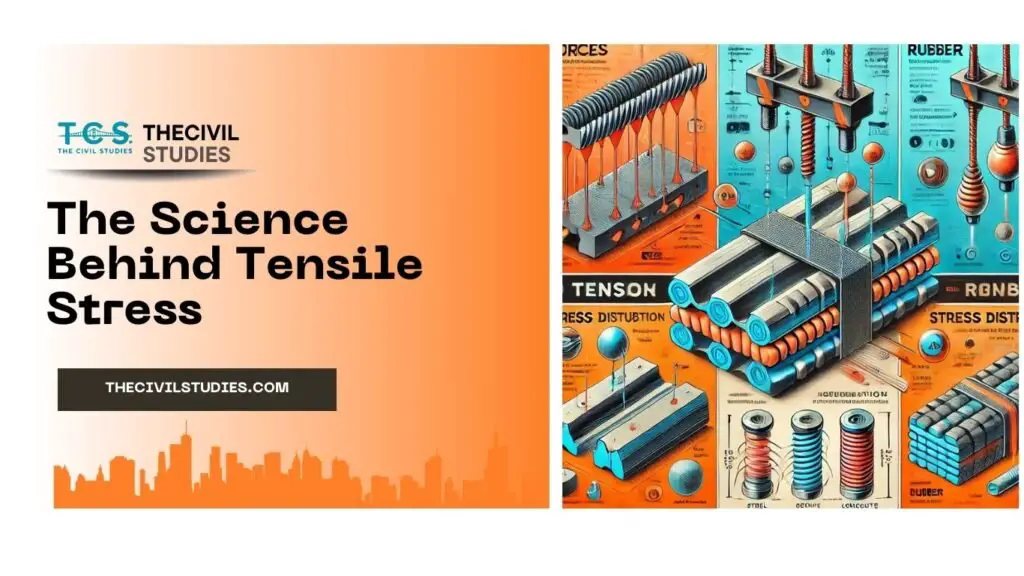
Least-Known Incident: The Hyatt Regency Walkway Collapse (1981)
One of the deadliest engineering disasters in the U.S. occurred in Kansas City when the Hyatt Regency hotel’s walkways collapsed, killing 114 people. A design change in the steel hanger rods doubled the tensile stress they had to bear, leading to their failure under the weight of people gathered on the walkway. This tragedy reshaped structural safety standards.
Mechanical Engineering – Ensuring Machine Reliability
Many mechanical components must resist tension to function properly. A single bolt under excessive tensile stress could cause an entire machine failure.
- Bolts and fasteners hold machines together under tension. Engineers design them with materials that have a high yield strength to prevent sudden failure.
- Gears and chains in heavy machinery endure tensile and shear forces, requiring hardened steel alloys to prevent wear and tear.
- Drive shafts in automobiles experience both tensile and torsional stress, making their material selection critical for durability.
Case Study: The Titanic’s Structural Failure
Investigations into the Titanic disaster (1912) revealed that the ship’s hull contained brittle steel with low tensile strength, leading to rapid fracturing when the iceberg struck. Modern shipbuilding now incorporates high-tensile steel alloys to prevent such failures.
Aerospace Engineering – Why Tension Matters at 30,000 Feet
In aerospace engineering, weight and strength must be perfectly balanced—materials need to withstand extreme tensile forces without adding unnecessary mass.
- Aircraft wings experience immense tensile stress on their undersides during takeoff and flight. Aluminum alloys, carbon fiber composites, and titanium are used to withstand these forces while staying lightweight.
- Fuselages and landing gear must endure tensile forces from cabin pressure, aerodynamic drag, and impact during landing. Any weak point could lead to catastrophic failure.
- Spacecraft and satellites face extreme temperature fluctuations, causing materials to expand and contract. Using tensile-resistant materials ensures long-term structural integrity.
Did You Know?
The Comet aircraft disasters (1950s) were due to undetected metal fatigue—tiny cracks developed under tensile stress, eventually leading to mid-air breakups. This led to the introduction of stress testing and fatigue analysis in modern aerospace engineering.
Automotive Engineering – Keeping Vehicles Safe Under Stress
Every moving car experiences tensile forces, whether during acceleration, braking, or an accident. Engineers design key components to handle these forces efficiently:
- Seat belts must resist extreme tensile forces during a crash, ensuring passenger safety. Modern seat belts use woven high-tensile polyester fibers to withstand sudden loads.
- Chassis and body panels must absorb tension and compression forces, requiring high-strength steel and aluminum alloys to prevent deformation.
- Suspension systems undergo tension while maintaining a smooth ride—springs and control arms must endure constant stretching and compressing.
Did You Know?
Formula 1 race cars use carbon fiber monocoques—lightweight yet highly tensile-resistant structures that keep drivers safe during high-speed crashes.
In India The Kolkata Metro Girder Collapse (2022)
One of India’s most significant tension-related failures occurred during the construction of the Kolkata Metro’s Howrah station. A pre-stressed concrete girder collapsed, killing one worker and injuring others. Investigations revealed that excessive tensile stress in the cables and improper tensioning contributed to the failure. This incident highlighted the critical need for quality control in pre-stressed structures and stricter adherence to safety standards in infrastructure projects.
The Stress-Strain Curve & Material Behavior
The stress-strain curve defines how materials respond to tensile forces:
1. Elastic Region:
- Material returns to its original shape when stress is removed.
- Follows Hooke’s Law: σ=Eε\sigma = E\varepsilon
- Example: Rubber bands stretch but return to shape.
2. Yield Point:
- The stress at which permanent deformation begins.
- Example: A metal wire permanently stretches after excessive pulling.
3. Plastic Region:
- Material deforms permanently but can withstand additional stress.
- Example: Plastic bottles deform but don’t break immediately.
4. Ultimate Tensile Strength (UTS):
- Maximum stress a material can endure before failure.
- Example: Titanium in aerospace for high strength-to-weight ratio.
5. Fracture Point:
- The material breaks due to excessive tension.
Example: Brittle materials like glass break suddenly.
Real-World Applications of Tension
- Bridges: Steel cables in suspension bridges handle continuous tensile stress (e.g., Howrah Bridge).
- Aircraft: Wings and fuselages endure high tensile stress during flight.
- Reinforced Concrete: Steel rebars prevent cracks in buildings and roads.
- Pre-Stressed Beams: Used in bridges and metro systems to enhance durability.
- Sports Gear: Tennis racquet strings and climbing ropes resist stretching forces.
- Seat Belts: Designed to absorb high tensile stress in accidents.
- Medical Implants: Artificial tendons and prosthetics withstand body movements.
Testing Methods for Tension in Materials
- universal Testing Machine (UTM): Measures tensile strength, elongation, and failure points by applying controlled force.
- Non-Destructive Testing (NDT): Uses ultrasound, X-rays, and magnetic methods to detect internal flaws without damaging the material.
- Dynamic Tensile Testing: Evaluates material behavior under varying loads and high-speed impacts to simulate real-world conditions.
- Strain Gauges: Measure deformation and stress distribution in structural components.
- High-Temperature Tensile Testing: Assesses material performance under extreme heat conditions, essential for aerospace and power plants.
Key IS Codes and Standards for Tension Testing
- IS 1608: Defines methods for tensile testing of metals, ensuring standardized mechanical property evaluation.
- IS 2062: Specifies the tensile strength and elongation requirements for structural steel used in construction.
- ASTM E8: International standard for tensile testing of metallic materials, widely used for quality assessment.
- BS EN 10002-1: European standard outlining procedures for determining the tensile properties of metals.
- IS 1786: Covers tensile strength requirements for high-strength deformed steel bars used in reinforced concrete.
- IS 432: Specifies tensile testing for mild steel wire rods used in construction applications.
Frequently Asked Questions (FAQs) on Tensile Stress & Tension in Materials
What is tensile stress, and why is it important?
Tensile stress is the force per unit area applied to stretch a material. It is crucial in engineering to ensure structures and machine components can withstand pulling forces without failure.
How is tensile stress different from compressive stress?
Tensile stress pulls a material apart, while compressive stress pushes it together. Materials must be designed to handle both types of forces depending on their application.
What is the formula for tensile stress and strain?
Tensile Stress (σ) = Force (F) / Area (A)
Strain (ε) = Change in Length (ΔL) / Original Length (L)
What is the difference between tensile strength and yield strength?
Tensile strength is the maximum stress a material can handle before breaking. Yield strength is the stress at which a material begins to deform permanently.
What is Young’s modulus, and why is it important?
Young’s modulus (E) measures a material’s stiffness, showing how much it deforms under tension. Higher values indicate greater resistance to stretching.
What is Hooke’s Law, and how does it relate to tension?
Hooke’s Law states that stress is directly proportional to strain within the elastic limit: σ = Eε. It helps predict how materials behave under small loads.
What are the key stages of the stress-strain curve?
- Elastic Region – Material returns to its original shape.
- Yield Point – Permanent deformation begins.
- Plastic Region – Material stretches but doesn’t break.
- Ultimate Tensile Strength (UTS) – Maximum stress before failure.
- Fracture Point – The material breaks.
What is the difference between ductile and brittle failure?
- Ductile failure: Material stretches before breaking (e.g., steel).
- Brittle failure: Material breaks suddenly without warning (e.g., glass).
How is tensile strength tested in materials?
Tensile testing is done using a Universal Testing Machine (UTM), which applies force until the material breaks, measuring stress, strain, and elasticity.
What are some common materials with high tensile strength?
- Steel – Used in buildings and bridges.
- Titanium – Essential for aerospace applications.
- Carbon fiber – Lightweight and strong for sports and automotive.
What are the key standards for tensile testing?
- IS 1608 – Tensile testing of metals.
- IS 2062 – Structural steel requirements.
- ASTM E8 – Tensile testing for metallic materials.
How does temperature affect tensile stress?
High temperatures weaken materials, reducing tensile strength, while low temperatures can make some materials more brittle and prone to sudden failure.
How does tension play a role in bridge construction?
Suspension bridges use steel cables to handle tensile forces, ensuring structural stability while supporting heavy loads and resisting environmental forces.
Why is tensile strength important in aerospace engineering?
Aircraft wings and fuselages experience extreme tensile stress during flight, requiring materials like titanium and composites to maintain strength while being lightweight.
How do engineers prevent tensile failure in buildings?
Reinforced concrete uses steel rebars to resist tension since concrete alone is weak in tension but strong in compression.
Discover more from
Subscribe to get the latest posts sent to your email.